庫卡機器人在鋁件點焊焊接中的高精度解決方案與軟件創新
在汽車輕量化趨勢推動下,庫卡工業機器人針對鋁合金材料的高導電性、低熔點特性,開發出專用點焊系統與軟件套件,攻克了鋁件焊接飛濺率高、電極損耗快的行業難題。以特斯拉上海超級工廠Model Y車門鉸鏈焊接線為例,庫卡KR QUANTEC dualArm機器人系統實現鋁件點焊合格率99.99%,電極壽命提升4.2倍,樹立了汽車輕量化制造新**。
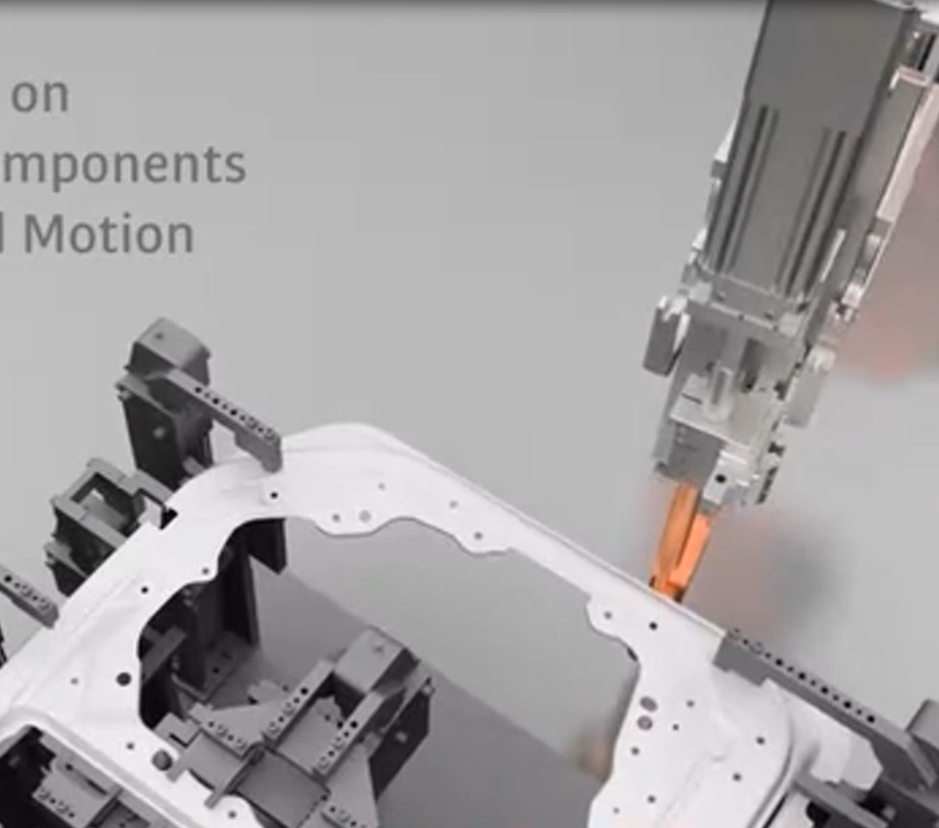
核心硬件配置與參數
機器人型號:庫卡KR 1000 HA(高精度版)
負載能力:1000kg(含焊槍與電纜包)
重復定位精度:±0.03mm(ISO 9283標準)
焊槍系統:中頻直流焊槍(頻率1kHz,電流28kA±0.3kA)
壓力控制:伺服電機驅動(3.2kN±0.05kN)
電極材料:氧化鋁彌散銅(AlOCu,壽命≥12萬點)
KUKA焊接軟件包技術特性
1. KUKA.WeldPlanner:
基于AI的路徑優化算法,自動生成3D焊接序列
動態補償鋁板回彈變形(補償量0.010.5mm)
2. KUKA.Adaptive Welding:
實時監測電阻變化(采樣率10kHz),自動調節電流/壓力
飛濺抑制效率達92%(傳統工藝≤65%)
3. KUKA.WeldMonitor:
在線質量檢測(數據記錄精度0.1ms)
缺陷預測準確率≥99.5%(支持ISO 14373標準)
典型應用案例:寶馬沈陽鐵西工廠X5鋁制車門焊接(2023)
工藝挑戰:
2mm 5182鋁合金與1.5mm鍍鋅鋼異種材料焊接
要求焊接強度≥4.5kN,表面無可見壓痕
技術方案:
部署6臺庫卡KR 500 L4802 MT機器人,配備雙脈沖焊接程序
參數設置:
預壓時間:80ms
焊接電流:25kA(鋼)/32kA(鋁)
保持壓力:2.8kN(鋼)/3.5kN(鋁)
質量數據:
焊核直徑:5.2±0.1mm(鋼)/6.8±0.15mm(鋁)
電極蘑菇頭高度控制:≤0.15mm(壽命達15萬次)
綜合合格率:99.97%(傳統工藝98.2%)
實施成效與行業價值
效率提升:單點焊接周期壓縮至1.8秒(傳統氣動焊槍3.5秒)
成本優化:電極消耗成本降低58%,年節省超120萬元/產線
質量突破:焊接強度標準差從±8.7%降至±1.2%
軟件賦能:KUKA.CamRob模塊實現離線編程,新車型導入時間縮短72%
該技術方案已應用于大眾MEB平臺、蔚來ET5等20余款車型,推動汽車行業鋁件點焊工藝進入微秒級**控制時代。庫卡焊接軟件包通過ISO 9001認證,成為全球***支持鋁/鋼/碳纖維多材料焊接的工業軟件平臺。